What is Weaving in Textile?
In the textile sector, weaving is the result of interlacement between two different sets of yarn that means warp and weft yarn. The fabric which is produced by using this interlacement technique is known as woven fabric. Weaving is the manufacturing process of woven fabric.
The weaving process is a fundamental textile manufacturing method used to produce fabric by interlacing two sets of yarns at right angles to each other. This method has been used for centuries and remains one of the primary ways to create fabric.
Difference Between Woven and Weaving:
In various textile interviews, one question has to ask by the recruiter that, “what is the difference between woven and weaving? There are so many who delivered the wrong answer in this case. The actual answer is that woven are one kind of fabric that is produced by interlacing warp and weft yarn and the process of woven fabric manufacturing is termed as weaving.
Flow Chart of Woven Fabric Manufacturing:
The actual process flow chart of weaving or woven fabric manufacturing has presented the below:
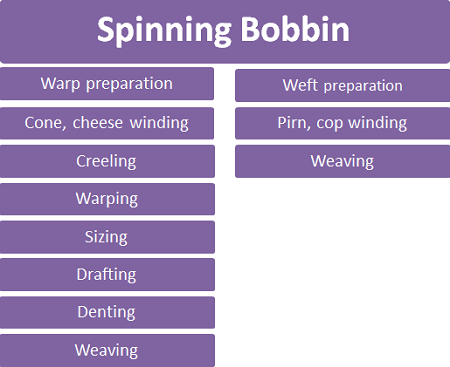
All the above processes have discussed below:
Warp preparation:
The main purpose of warp preparation is to transfer yarn to a weaver’s beam from the spinner’s package which can be placed behind a loom ready for woven fabric manufacturing. Normally, a weaver’s beam contains at least a few thousands of ends.
Cone, cheese, pirn, cop winding:
It is a method of transferring yarns from cones, hank, and bobbins into a suitable form of package. Here, the length of the yarn should be longer. Normally this process is used to form a single yarn package which will be suitable for the next processes.
Creeling:
It is the placement of full packages in a position that is ready to be unwound as part of the transfer operations. In another word, it is the removal of the exhausted packages and their replacement with full ones.
Warping:
The parallel winding of warp yarn from so many winding packages such as cone, cheese, pirn, cop, etc. into warp beam is known as warping.
Sizing:
It is the process of applying protective adhesive coating on the yarn surface is termed as sizing. Sizing increase the yarn strength, elasticity of yarn, weight of yarn, etc.
Drafting:
In the textile weaving sector, it is known as the selection of harnesses or heald frames for individual warp yarn according to the design.
Denting:
In the woven fabric manufacturing industry, denting means drawing the warp yarn through the dent as required by the reed plan. Denting determines more perfectly the width of the woven fabric and the ends per centimeter (EPI).
Types of Looms in Weaving:
1. Handloom: Traditionally used for hand-weaving fabric, especially in artisanal production.
2. Power Loom: Mechanized looms used in factories, which significantly increase the speed and efficiency of weaving.
3. Shuttleless Looms: Modern looms (such as rapier, air-jet, and water-jet looms) that don’t use a shuttle to insert the weft, resulting in faster production rates.
Weave Patterns:
- Plain Weave: The simplest and most common weave pattern where the weft alternates over and under the warp yarns.
- Twill Weave: Produces diagonal lines in the fabric, known for its durability (e.g., denim).
- Satin Weave: Characterized by a smooth surface with long floats of yarn, creating a shiny fabric.
Importance of Weaving Process:
Weaving is central to textile production, and its efficiency directly impacts the quality, texture, and performance of the fabric. From clothing to industrial textiles, the weaving process is essential in creating a wide range of products.